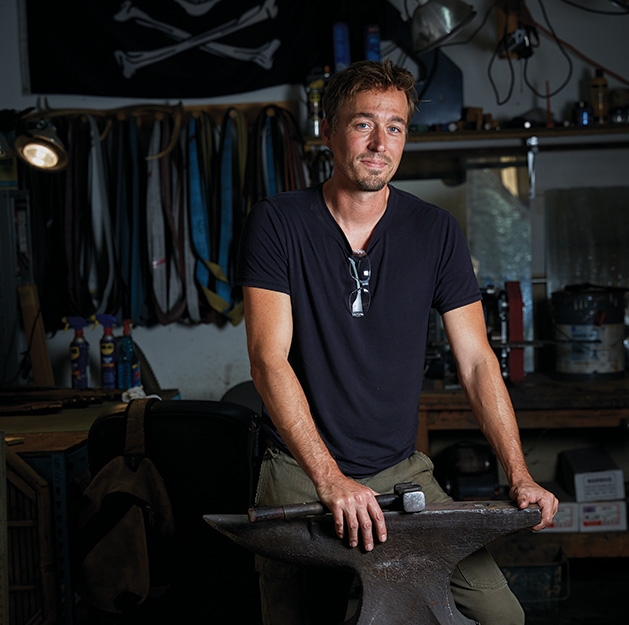
Bladesmith Jason Kraus suspects that each knife he’s forged has some of his blood in it.
“They’re razor sharp, and they’ll cut you when you don’t even know it,” Kraus says. “I’m getting better at not cutting myself, but you will get burned in knife making, and you will get cut. Fortunately, I have all my digits.”
Bladesmithing, the skill of using fire to forge steel into knives, is both the 38-year-old Mound native’s passion and profession.
Since 2011, Kraus has hand-crafted custom-made knives, swords, jewelry, knife accessories, and even decorative roses at his business, Northstar Forge in Carver. His bladesmithing abilities were on display when he competed on the History Channel’s Forged in Fire in 2017 and the Discovery Channel’s Master of Arms last year.
“Those shows are fun to watch, and it gets a lot of people asking if there is someone that makes knives” close to where they live, says Kraus, who made his own version of a 1913 Patton cavalry saber on Master of Arms. “It’s such a primal skill. Humans can do so much with just a blade. It’s such a huge part of us.”
Kraus describes his blades as “sharp art,” his distinctive style as “perfectly imperfect, simplistic beauty, ruggedly refined.”
“I’m more like an artist than anything—even though my knives are all functional,” he says. “You could go chop down a tree if you want with my Bowie knife, even though it looks as if you wouldn’t want to scratch it.”
Luke Dellmyer, a bladesmith from Hellertown, Pa., praises Kraus for his knives’ blend of vintage looks with a modern touch. “There’s not a lot of guys who are doing that,” says Dellmyer, who befriended Kraus while both were on Master of Arms. “His work is pretty exceptional in the field. He just needs to get recognized more, and there should be no reason he shouldn’t be at the top of the game.”
Origins
Kraus has always been fascinated by knives and the outdoors. He remembers getting his first knife when he was 5 (a Swiss Army knife the exact model used by TV’s MacGyver) and spent much time in his teens exploring the woods surrounding his house in Jordan.
“That’s where I liked to be all the time,” he says. “I would go test out knives, and use machetes to cut through the forest.”
But, it wasn’t until years later when his wife, Allison, asked him what he would love to do with his life that he seriously contemplated a career making knives and swords. Kraus had his own house painting business (not his dream job, he admits), while Allison was launching her business—Shoreline Insurance Group in Excelsior.
“He’s a kid at heart, and he’s super creative, so it made sense,” Allison says. “But, in my mind, I’m thinking, ‘Isn’t that what you do when you retire? So, let’s keep thinking.’”
By chance, Allison’s friend told her of seeing a segment on CBS Sunday Morning featuring renowned bladesmith Bob Kramer. The friend saw similarities in Kramer’s story to Kraus. Like Kramer, Kraus had struggled with dyslexia.
“It really limited my abilities to what college courses to take,” Kraus says. “I’m not very good at school, but I’m good with my hands.”
After watching the program, Allison’s friend told her that Kraus should make knives—not knowing Kraus mentioned it earlier. “[Allison] was like, ‘That’s what he said,’” he says. “It was an odd coincidence.”
That convinced Allison, and she emailed Kramer, asking for advice on what Kraus should do next. He recommended a two-week introduction class by the American Bladesmith Society in Arkansas. “I went and took that, and I was off,” he says. “It was life-changing.”
Kraus soon learned that many of his perceptions on how knives are actually made were off target.
“I thought you grab steel, any steel, and you can forge it and hammer on it and put an edge on it and call it a day,” he says. “They taught me about the metallurgy of the different types of steels that you want to look for as well as the capabilities of how a knife should be able to perform.”
Enjoying His Craft
Kraus revels in being able to express himself in so many different ways as a bladesmith—whether it be forging the blade, crafting the wood handle or making the leather sheath.
“I could live five lifetimes and still not be able to do everything I want to try and know and understand [with bladesmithing],” he says.
Most of his advancement in the field is self-taught, he says. After the class in Arkansas and another on making handles and hand guards, he didn’t take another one for about five years.
“It was just trial and error and reading books,” says Kraus, who plans to test for his Journeyman Smith designation next year. “There wasn’t even a lot of YouTube back then. Now I call it the University of YouTube, and knife-making is exploding.”
To craft many of his hunting, kitchen or Bowie knives, Kraus uses high-carbon steel or the multi-layered Damascus steel, which is made by forging different types of steel to form a pattern like a topographical map. For some custom knives, he will repurpose railroad spikes and leaf springs from older vehicles.
Prices for his knives range from $200 or so for a railroad spike knife to $2,000 to $5,000 for a sword, he says. He says the popularity of the TV show Game of Thrones prompted a few sword inquiries, but most were scared away by the price. (He says the fictional Valyrian steel swords on the show are made of Damascus steel.)
How long it takes Kraus to forge a knife depends on the blade. For instance, a drop-point hunter knife (one a deer hunter would carry) takes about four days to complete. A Scottish dirk knife presented by a groom to his new wife on their wedding day took him nearly a month.
“It’s all the time and the intricacies of each knife, such as the size and the handle material types,” says Kraus, who also offers tutorships to the craft at his forge. “That’s where all the value comes in.”
People who buy his knives run the gamut from big game hunters to people looking for high-performing cutlery in their kitchen. “I’ve had people who hunt elk come back with antlers that weren’t necessary nice enough to put up on the wall,” he says. “I’ll use an antler in the handle of a knife. It usually ends up [displayed] on a shelf, which is an insult and a compliment all at the same time.”
Kraus also makes some jewelry, notably Damascus steel wedding rings. “I’ve had husbands and wives want a pair of rings forged from the same billet of steel,” he says.
Kraus spends a lot of time on the road, getting his name and his brand out among other bladesmiths and consumers. He admits it’s not easy to make a living.
“I’m starting to get there, though,” he says. “Once you get that journeyman [status], your name, quality, and the product gets more recognized. I’ve had a lot of support from Minnesotans in general. They really get behind their artists.”
Northstar Forge
104 Sixth St. W., Carver
Facebook: Northstar Forge
Instagram: @northstar_forge
YouTube: Jason K